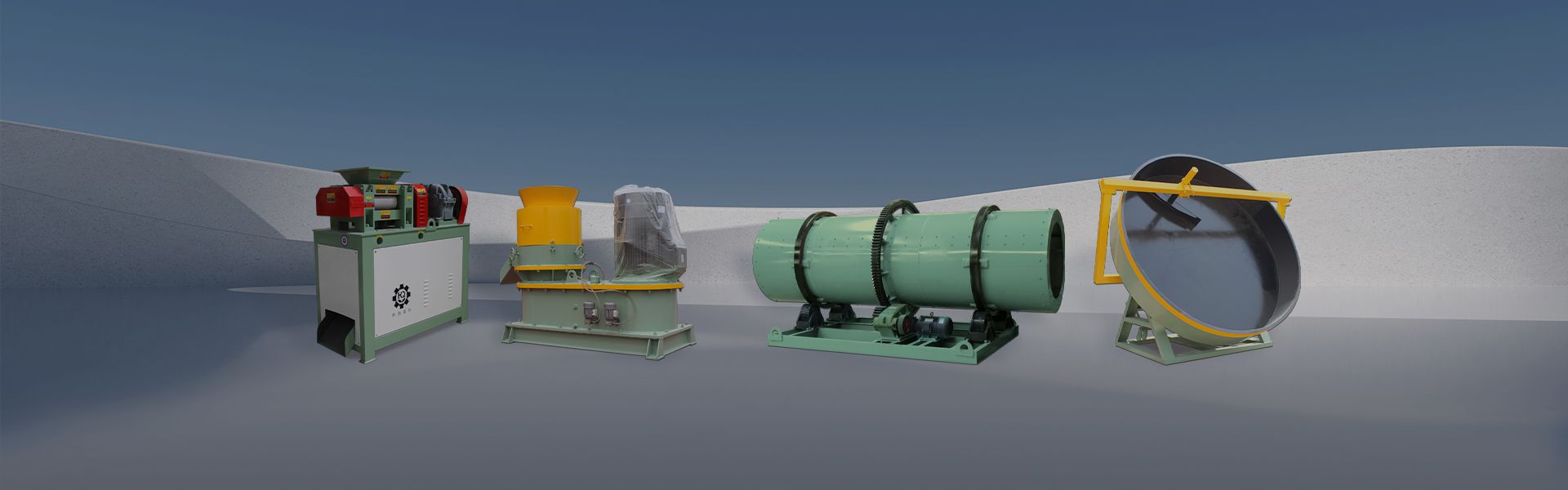
Hydraulic roller granulator is an efficient equipment that uses hydraulic technology for material granulation. It mainly applies high pressure to the material through two sets of relatively rotating pressure rollers, causing the material to undergo plastic deformation and bond into particles under high pressure. This granulation method is suitable for various materials, especially in industries such as fertilizers, chemicals, metallurgy, etc. It has a wide range of applications.
The hydraulic roller granulator is suitable for processing various dry powders, slightly wet powders, and partially viscous materials, including but not limited to:
Fertilizer industry: granulation of compound fertilizers, phosphate fertilizers, potassium fertilizers, etc.
Chemical industry: granulation of catalysts, dyes, additives, etc.
Metallurgical industry: granulation of iron powder, mineral powder, etc.
Food industry: granulation of seasonings, additives, etc.
The structure of the hydraulic roller granulator mainly includes the following parts:
Roller assembly: consisting of two sets of relatively rotating pressure rollers, it is the core component in the granulation process. By adjusting the distance and pressure between the pressure rollers, the size and density of the particles are controlled.
Hydraulic system: provides stable high pressure for the pressure roller, ensuring the continuity and stability of the granulation process.
Feeding system: used to uniformly and continuously feed materials between the rollers.
Control system: including monitoring and adjustment of parameters such as pressure, speed, temperature, etc., to ensure precise control of the granulation process.
Rack and support: Provide stable support to ensure the smoothness and safety of equipment operation.
Crushing and screening system (optional): used to process non-conforming particles generated during the granulation process, ensuring product consistency.
Material pretreatment: Firstly, the material needs to undergo pretreatment, including crushing, screening, and appropriate mixing, to ensure the uniformity and suitable particle size of the material, as well as control the humidity and viscosity of the material to make it suitable for the granulation process.
Feeding and conveying: The pre treated material is evenly fed into the rollers of the granulator through the feeding system. Accurate control of the feeding system is crucial for ensuring uniform distribution of materials and continuity of the granulation process.
High pressure squeezing: When the material enters between the rollers, the hydraulic system provides stable pressure, allowing the two sets of rotating rollers to apply high pressure to the material. Under high pressure, the material undergoes plastic deformation, the distance between molecules decreases, the gaps between material particles are compressed, and the material is bonded and formed under high pressure.
Particle formation and discharge: Under the squeezing effect of the roller, the material gradually forms continuous strips. As the roller rotates, the strips are squeezed out and naturally break into particles. These particles typically have high hardness and stability, making them suitable for subsequent processing or direct application.
Cooling and post-treatment (optional): For certain materials, the granulated particles may need to be cooled to stabilize the particle structure and prevent deformation or adhesion due to high temperatures. The cooled particles can also be processed through a crushing and screening system to remove unqualified particles, ensuring the quality of the final product.
Efficient granulation: By precisely controlling the pressure and speed of the rollers, the material can be efficiently extruded into uniform particles.
High particle quality: The material particles after granulation have good hardness, stability, and uniformity, meeting the quality requirements of different industries.
Wide applicability: Suitable for granulation of various dry powder and slightly wet materials, with strong adaptability to materials.
High degree of automation: equipped with advanced control systems, easy to operate and maintain.
Low energy consumption: The high efficiency of the hydraulic system and the continuity of the granulation process result in overall low energy consumption.
Environmental protection: The granulation process generates low dust and noise, with minimal impact on the environment.
© Copyright 2024. All Rights Reserved.