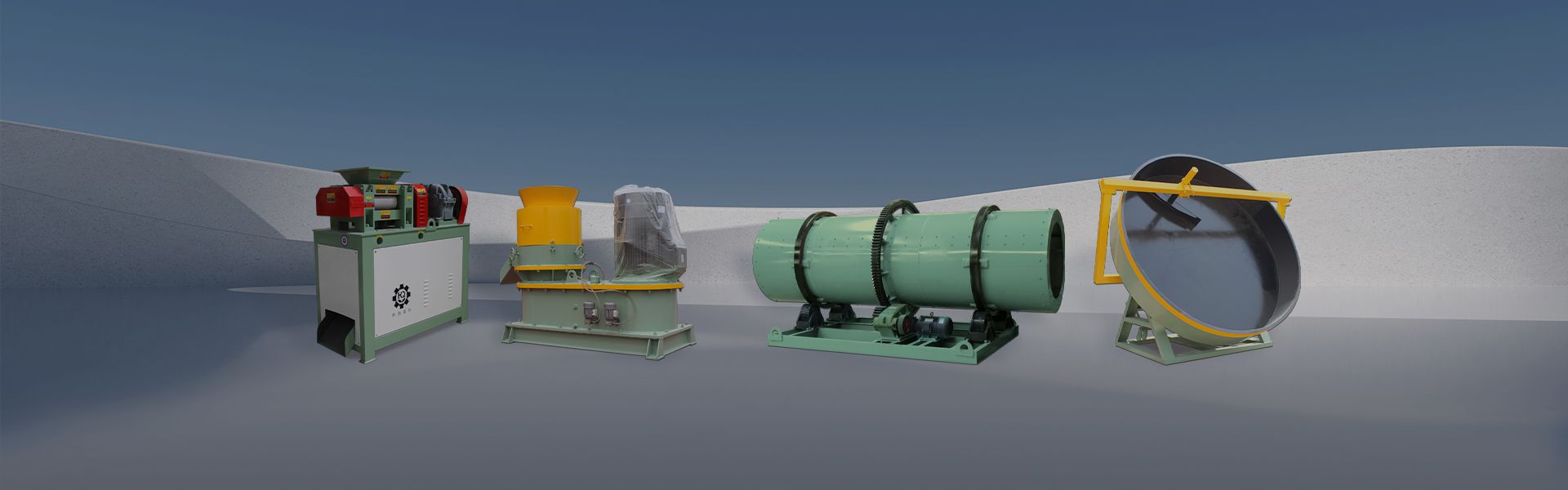
The new type of organic fertilizer granulator is an efficient granulation equipment designed specifically for organic fertilizer production. It combines modern granulation technology and environmental protection concepts, and can convert various organic wastes (such as livestock manure, crop straw, food processing waste, etc.) into high-quality organic fertilizer particles. The emergence of this device not only solves the problem of organic waste disposal, but also promotes the sustainable development of agriculture.
The new type of organic fertilizer granulator is widely used for the treatment and reuse of organic waste generated in agriculture, animal husbandry, food processing industry, etc., including:
Livestock and poultry manure: chicken manure, cow manure, pig manure, etc.
Crop waste: straw, rice husks, corn cobs, etc.
Food processing by-products: fruit peels, vegetable residues, coffee grounds, etc.
Garden waste: leaves, branches, etc.
The structural design of the new organic fertilizer granulator usually includes the following key parts:
Feeding system: used to evenly feed pre treated organic materials into the granulator.
Granulation system: The core granulation components, such as flat molds, ring molds, extrusion drums, etc., press materials into shape through high pressure or rotational force.
Cooling and drying system: Ensure that the organic fertilizer particles after granulation can be quickly cooled and dried to improve the hardness and stability of the particles.
Crushing and screening system: used to crush oversized or unqualified particles to ensure the consistency of the final product.
Control system: including monitoring and adjustment of temperature, pressure, humidity and other parameters to ensure efficient and stable granulation process.
Material pretreatment: Firstly, it is necessary to pretreat organic waste, including crushing, mixing, and adjusting humidity appropriately. The purpose of pretreatment is to achieve the required particle size and humidity for granulation of materials, and to improve their plasticity and adhesion.
Feeding and conveying: The pre treated material is uniformly fed into the main working area of the granulator through a feeding device, which usually includes one or more extrusion components such as flat molds, ring molds, or extrusion drums.
Squeezing granulation: Inside the granulator, the material is subjected to high pressure or rotational force, and is forced to pass through the holes or gaps of the extrusion components. During this process, the plastic deformation of the material and the bonding between particles shape it into particles with a certain shape and size.
Cooling and drying: Organic fertilizer granules that have just been pelletized have a high temperature and require rapid cooling through a cooling system to stabilize the particle structure and prevent deformation. Subsequently, the excess moisture in the particles is further removed through a drying system to improve the hardness and stability of the particles.
Screening and post-processing: The cooled and dried particles need to be screened to remove unqualified particles (such as oversized or undersized particles). Qualified particles after screening can be packaged or further processed as needed, such as adding nutrients, microorganisms, etc.
Compared with traditional granulation equipment, the new organic fertilizer granulator has the following significant characteristics:
Efficient and energy-saving: adopting advanced granulation technology, low energy consumption, and high production efficiency.
Environmentally friendly and pollution-free: The granulation process produces less dust, low noise, and is environmentally friendly.
Strong adaptability: able to handle a variety of organic waste, with a wide range of applications.
Good particle quality: Through precise control of the granulation process, the organic fertilizer produced has uniform particles, moderate hardness, and good solubility.
High degree of automation: equipped with advanced control systems, easy to operate and maintain.
Significant economic benefits: not only does it solve the problem of organic waste disposal, but it can also be converted into valuable organic fertilizers, achieving resource recycling.
© Copyright 2024. All Rights Reserved.