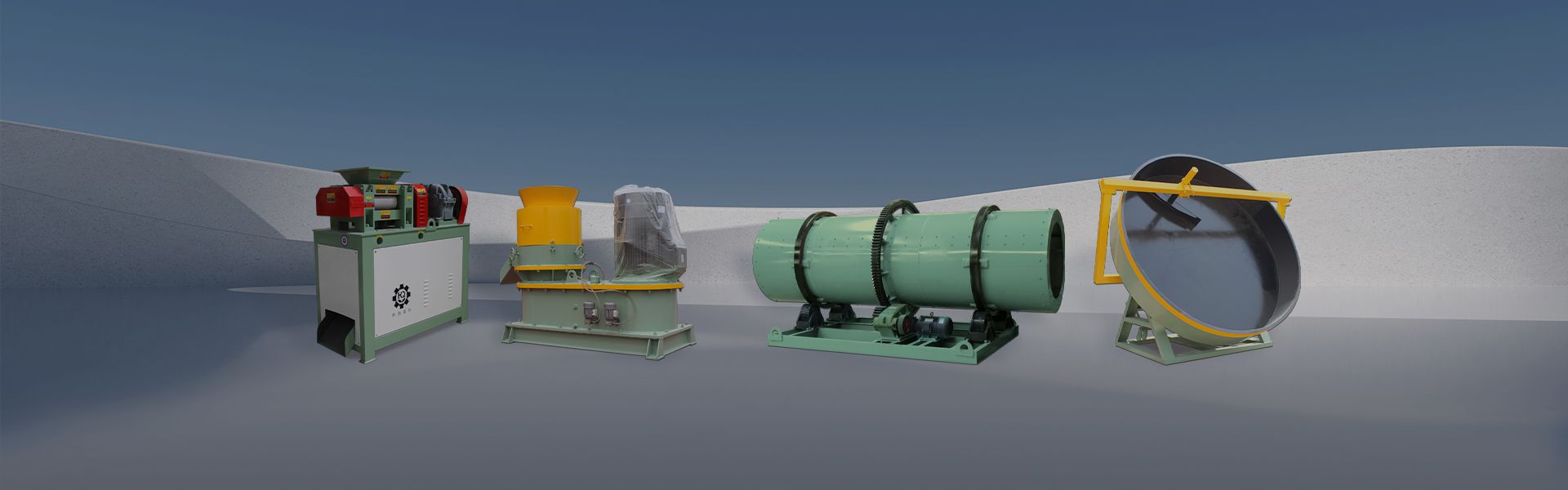
The disc granulator production line is a widely used production system in the fertilizer, chemical, food and other industries, which is used to form spherical or approximately spherical particles from powdered or fine-grained materials through the centrifugal force of rotating discs and the frictional force between materials. This production line has become the preferred granulation process for many industries due to its efficient granulation capacity, flexible raw material adaptability, and stable granulation effect.
The disc granulator production line mainly consists of the following equipment:
Raw material preparation equipment: including crushers and screening machines, used for pre-treatment of raw materials to ensure uniform particle size and remove impurities.
Mixing equipment: used to mix raw materials with adhesives or water evenly, improving granulation efficiency and particle quality.
Disc granulator: The core equipment generates centrifugal force through the rotation of the disc, and the material rolls on the inner wall of the disc, rubbing against each other, gradually forming spherical particles.
Spray system: during the granulation process, appropriate amount of water or adhesive is sprayed into the disc through the spray system to control the humidity and stability of particles.
Drying equipment: After granulation, the particles need to be dried with a dryer to remove excess moisture and improve their stability.
Cooling equipment: The dried particles are cooled by a cooling machine to prevent deformation caused by high temperatures.
Screening equipment: used to screen out particles that meet the particle size requirements, remove particles that are too large or too small, and ensure product quality.
Packaging equipment: Automatic packaging machine is used to weigh and package finished granules.
Control system: including PLC control system, used to monitor and adjust key parameters in the production process, ensuring the stability of the production process and product quality.
1. Raw material preparation
Raw material crushing and screening: Raw materials (such as fertilizer raw materials, chemical raw materials, etc.) are first crushed to a particle size suitable for granulation by a grinder, and then large particles and impurities are removed by a screening machine to ensure uniform particle size of the raw materials.
Raw material mixing: Mix the crushed raw materials evenly with binders, additives, etc. as needed to improve granulation efficiency and particle quality.
2. Granulation
Disc granulation: The prepared raw materials are fed into a disc granulator, where they gradually form spherical or approximately spherical particles through mutual friction and bonding between the materials under the rotational force of the disc. During this process, the spray system will spray appropriate amount of water or adhesive as required to control the humidity and stability of particles.
3. Drying
Particle drying: After granulation, the particles need to go through a dryer to remove excess moisture, in order to improve the stability and storage of the particles. The drying process requires precise control of temperature and time to avoid particle deformation or adhesion.
4. Cooling
Particle cooling: The dried particles are cooled to room temperature or a suitable temperature by a cooling machine to prevent a decrease in particle quality caused by high temperatures.
5. Screening
Particle screening: Use a screening machine to screen out particles that meet the particle size requirements, remove particles that are too large or too small, and ensure the consistency and quality of the finished particles.
6. Packaging
Finished product packaging: The screened finished product particles are weighed and packaged by an automatic packaging machine, ready for storage or shipment.
7. Control and Monitoring
Automation control: Production lines are usually equipped with PLC control systems to monitor and adjust key parameters in the production process, such as raw material ratio, granulation speed, drying temperature, etc., to ensure the stability of the production process and product quality.
Give us a call or drop by anytime, we endeavour to answer all enquiries within 24 hours on business days. We will be happy to answer your questions.
© Copyright 2024. All Rights Reserved.